ALIMENTATION HAUTE TENSION DE LABORATOIRE
Projet publié dans la revue LED n°185 et LED n°186 de septembre et novembre 2004 sous le titre "Alimentation Haute Tension de Laboratoire - Stabilité de 0,1% - 50 à 450 V / 500 mA"
L’alimentation que nous vous proposons délivre une tension réglable de 50 à 450 Volts sous un courant de 500 milliampères, avec une stabilité de 0,1 %
Ondulation résiduelle à 100Hz et facteur de bruit : <1 mV pp sur toute la gamme.
La résistance interne est < 0,5 Ω en statique et < 1 Ω en dynamique de 10Hz à 100KHz.
Mise en garde : La conduite de ce projet requiert expérience et professionalisme. Les tensions véhiculées sont toutes dangereuses, au même titre d’ailleurs que celles générées dans amplificateurs à tubes. Prudence donc !
Toutefois en procédant méthodiquement et en proscrivant tout montage de type "bidouille", le résultat est à la mesure des efforts.
Ce projet a été remanié en juin 2012 au niveau des circuits et des cartes. Les circuits présentés ici sont ceux de la nouvelle version.
Cette nouvelle version est directement compatible avec la version originale, elle ajoute un circuit de protection contre les courts circuits en sortie et une détection du claquage du ballast de la pré-régulation.
Les transistors ballast BUZ80 sont remplacés par les 2SK1120.
Les transistors 2N5401 sont remplacés par les MPSA92.
LE SCHEMA
Etude du schéma bloc
Le circuit se compose de 3 sous-ensembles : le circuit de commande, de pré-régulation et de régulation: Schéma bloc
Le circuit de commande délivre les tensions de +24 Vdc, +5 Vdc et -5 Vdc et permet la mise en service temporisée du transformateur principal de 400 VA.
La carte de pré-régulation délivre sous une impédance réduite (Z = 5 Ω), une tension stabilisée à 485 Vdc.
La carte de régulation délivre la tension variable régulée de 50 à 450 Volts sous un courant max de 500 mA.
Circuit de Commande
Le circuit de commande permet la mise sous tension ‘’en douceur’’ et fournit les diverses alimentations.
A la mise sous tension, seuls les deux petits transformateurs situés sur la carte sont actifs. Pendant 3 secondes , le transformateur de 400 VA est alimenté au travers d’une résistance de 330 Ω de 100 Watt ce qui permet la mise en charge des condensateurs, tout en protégeant le pont redresseur, les fusibles et les SIPMOS des sur-courants fatals.
La temporisation est issue de la charge différée de C1 qui appliquée à la broche 3 du 741 (IC1) fixe la sortie à 0 V pendant 3 secondes. Une fois la tension de C1 supérieure à celle présente sur la broche 2, la sortie du 741 bascule à 24 Vdc entrainant la fermeture du relais statique REL1. L’appareil est alors opérationnel.
Afin d’éviter les sur-courants en cas de coupure d’alimentation, deux composants sont ajoutés au circuit: La diode D1 qui décharge immédiatement C1 en cas de coupure secteur, et la résistance R2 de 100 Ω qui a le même effet en cas mise hors service de l’appareil par l’interrupteur (SW1).
L’interrupteur de mise sous tension est du type ‘’ON-ON’’ à 3 circuits (3RT).
Ainsi la mise hors-service via l’interrupteur suivie imédiatement de la remise en service imposera une nouvelle temporisation de 3 secondes.
Les tensions de +24 Vdc et – 5 Vdc sont celles qui conditionneront la stabilité de l’ensemble comme nous le verrons en analysant le circuit de régulation.
La mise en œuvre des régulateurs 78xx et 79xx nécesite quelques précautions.
Le bruit résiduel de sortie peut être réduit à moins de 100 µV si le tracé des pistes est bien étudié.
Ainsi sur la carte, le deux broches des condensateurs tampons (C3 et C2 pour le 7824 doivent impérativement se trouver entre celles du pont redresseur et le régulateur, le plan de masse se faisant au niveau de la broche de référence du régulateur.
Un condensateur de filtrage après redressement cablé hors du chemin direct vers le régulateur laisse se développer une ronflette de quelques millivolts.
De même les deux broches des condensateurs de filtrage (C5 et C4) doivent impérativement se trouver entre la broche de sortie du régulateur et la broche de sortie utile. Comme montré ici, les pistes doivent être les plus courtes possibles.
Une autre erreur est de placer juste à la sortie régulée un ‘’gros’’ condensateur (>1000 µF) afin d’écraser toute ondulation résiduelle. Mais cela entraine une instabilité du circuit qui peut se manifester par une oscillation de 300 à 600 Hz, dépendant de la valeur du condensateur. Le constructeur le précise dans ses ‘’Application Notes’’.
La tension de 24 Vdc alimente également le circuit d’alarme sonore et visuelle de surcharge en courant (R12 + Z2).
Le buzzer et la LED clignotante sont placés en série, ce qui a pour effet d’alterner le fonctionnement du buzzer au rythme du clignotement de la Led, provoquant un ‘’bip-bip’’ de type alarme assez dérangeant .
Le déclenchement de l'alarme est provoqué par la détection via D4 d'un courant de sortie qui dépasse 500 mA ou la détection via IC1B du claquage du ballast de la pré-régulation qui se met en court circuit.
La tension de d’alimentation des modules afficheurs est de 10Vdc, toutefois comme nous le verrons plus loin, il y a lieu de polariser ces modules au départ du –5Vdc de façon à permettre le fonctionnement différentiel des entrées.
Le relais statique est un CRYDOM type D2410 de 240 V / 10 A.
Ce relais est activé par une tension de 3 Vdc, et commute au passage par zéro du 230 Vac, ce qui réduit considérablement le parasitage des circuits.
Les trois thermiques placés respectivement sur les 3 radiateurs des MOS coupent tous les circuits à l’exception du ventilateur qui continue à assurer le refroidissement.
Circuit de pré-régulation
Le circuit de pré-régulation redresse la tension de 400 Vac et fournit une tension continue qui varie entre 540 et 600Vdc suivant les aléa du secteur et du courant fourni.
Le transistor Q1 est un MPSA92 et est monté en source de courant.
Le courant de 1 mA développe dans les résistances de collecteur (R5,R6,R9) une tension de 500 Vdc indépendante des variations du secteur.
Cette tension est filtrée par la cellulle RC (R8,C6) et appliquée sur la gate du 2SK1120.
Le courant de fuite de la gate est de l’ordre de 10 nA, ce qui pour une résistance de 220 kΩ occasionne une chute de tension de 2 mV.
Comme déjà écrit dans nos pages, les SIPMOS sont assez susceptibles, et doivent être bien entourés.
C’est la raison d’être des condensateurs et diodes suivantes: C4, C5, C6, C7, et D1.
La tension de sortie du pré-régulateur est ajustée à 530 Vdc.
La résistance interne de sortie est de l’ordre de 5 Ω.
L’ondulation résiduelle à 100 Hz est de 10 mVpp pour un courant de 500 mA.
Le SIPMOS de pré-régulation 2SK1120 dissipe au maximum une puissance de 35 W.
Une portion de la tension de sortie du pré-régulateur ajustée par le potentiomètre P2 est routée vers la carte de commande afin de s'assurer que la pré-régulation est bien fonctionnelle. En effet en cas de court-circuit franc à la sortie de l'appareil, ce ballast peut claquer malgré les temporisations et les protections. En cas de claquage, le ballast se met en court-circuit et la tension rejoint la tension d'entrée avant filtrage.
Le potentiomètre P2 est réglé à +11,8Vdc. En dépassant +12Vdc le circuit d'alarme de la carte de commande active la LED d'alarme et le buzzer.
Circuit de régulation
Nous retrouvons ici deux SIPMOS 2SK1120 (Q2,Q3) montés en ballast série afin de distribuer les dissipations. Ces transistors sont commandés par un troisième SIPMOS BUZ80 (Q1) monté en gate commune.
Le rapport de la résistance de source (R4) de 470 Ω et des résistances de charge du collecteur de Q1 (R5, R6) de 200 kΩ, nous donne un gain de 400.
Toutefois, une portion de la tension de sortie équivalente à 1/20 (R13+R14/R12+P2) est réinjectée en contre-réaction négative dans le circuit de gate de Q1 et nous réduit le gain total à 20.
Nous verrons plus loin les avantages de cette contre-réaction.
La tension de commande du premier ballast (Q3) est prélevée à la jonction des deux résistances de charge de Q1: R5 et R6, celle du deuxième ballast (Q2) au drain de Q1.
Une résistance (R22) de 22 kΩ / 50 W (R54) placée en sortie du circuit fait circuler un courant de 20 mA afin de positionner les ballasts hors de leur caractéristique non linéaire de départ (Caractéristique de transfert Vgs/Id). Cette résistance dissipe en fait 11 W, mais une résistance de 50 W a été choisie à cause de sa caractéristique d’isolation de 750 dc avec son enveloppe métallique. (Datasheet)
Le réglage de la tension est obtenu au curseur du potentiomètre 10 tours P50 de 10 kΩ.
Après filtrage (R2,C6) la tension est injectée sur l’entrée positive du 1er MC1458 (IC1A). Ce circuit est monté en gain unitaire, et sa sortie est réglable dans une plage de 20 Vdc. Cette tension appliquée sur la source de Q1 via R4 fait varier la tension de sortie dans une plage de 400 V.
Les résistances R1 et R3 sont calculées pour permettre une plage réglable de 50 à 480 Vdc. Une portion de la tension est prélevée pour l’afficheur ‘’Tension’’ par le potentiomètre P2. La tension au curseur varie de 0 à 45 mV.
Le courant parcourant R15 (0,22 Ω) développe une tension aux bornes de P3. Lorsque le courant dépasse 500 mA, cette tension s’élève à 110 mV et fait basculer la sortie du 2ème MC1458 (IC1B) de +24 à 0 V et déclenche l’alarme de surcharge (LP5 + buzzer)
Le potentiomètre P1 permet d’ajuster le déclenchement de cette alarme à partir de n’importe quel courant.
Une portion de la tension développée en P3 (0 à 50 mV) est envoyée vers l’afficheur ‘’Courant’.
Le circuit composé de R18-P4-D2 et Q4 limite le courant en bloquant le dernier ballast. P4 est ajusté pour que cette limitation entre en fonctionnement pour un courant supérieur à 500 mA.
Ce circuit limite également "la casse" en cas de court-circuit franc en sortie de l'appareil.
Choix des transistors ballast
Le choix des transistors ballast s’est porté sur le 2SK1120 disponible sur le marché. Ce SIPMOS est un N channel en boitier TO247, supporte 1000 V de tension D-S et peut dissiper 150 W à condition d’être bien refroidi. (Carctéristiques principales)
Ces transistors restent de par leur conception assez ‘’susceptibles’’. Le circuit et le dessin des cartes ont été étudiés de nombreuses fois avant d’aboutir à un résultat satisfaisant. Vous noterez le luxe de précautions qui entoure ces transistors : diodes anti-retour sur tous les contacts, capacités anti-surtension, résistances d’amortissement dans les portes …
Les transistors utilisés pour cette réalisation sont des Infineon, Siemens ou des Toshiba. Des succédanés chinois se sont révélés inutilisables pour cette application.
Modules afficheurs
Les modèles choisis sont des PM-128 ou PM-128BL du fabricant chinois ‘’Huayi’’ disponibles en France (voir en fin d’article).Il y a lieu d’enlever les pontages pour supprimer le point décimal, et fixer la sensibilité à 199,9 mV à fond d’échelle.
La portion de HT prélevée sur le trimmer P2 varie de 5 à 45,0 mV pour 50 à 450 Vdc .
Le courant prélevé sur l’ajustable P3 varie de 0 à 50,0 mV pour 0 à 500 mA.
Nous avons alors un affichage à 3 digits (000 à 450 V ou 500 mA)
La précision des modules afficheurs est spécifiée à +/- 0,5%, mais en pratique, il faut compter plutôt sur +/-1%.
La surprise vint du fait que la notice des distributeurs présentait ce mètre comme ayant une masse flottante. Or la première mise en œuvre prévoyait une alimentation de 10 Vdc, référencée à la masse générale (0 V), mais la masse du module tout en étant ‘’flottante’’ bloque le circuit d’entrée du mètre si on fixe celle-ci au 0 V. En fait, l’entrée du DPM est différentielle, et pour fonctionner correctement, celle-ci doit ‘’flotter’’ entre 0 et +10 Vdc, de préférence au milieu. La solution fut de déporter le pôle d’alimentation négatif du module afficheur au -5 Vdc, l’alimentation positive étant de +5 Vdc. L’entrée différentielle travaillant autour du 0V fonctionne alors normalement.
Protections
L’ensemble de la réalisation est protégé en intensité par 3 fusibles : 2 ampères en tête de secteur, 1 A à l’attaque du redresseur HT et un 500 mA rapide à l’entrée du régulateur. Chaque fusible est monitoré par un voyant néon en cas de claquage.
Un courant supérieur à 500 mA, active un avertisseur lumineux clignontant et déclenche un signal sonore strident (et insupportable).
Un ventilateur assure un refroidissement forcé de tout l’appareil.
Trois capteurs thermiques placés sur chacun des refroidisseurs coupent l’alimentation en cas de surchauffe. Le ventilateur seul continuera à fonctionner. Le chassis et la mise à la terre par le cordon secteur sont raccordés par une borne indépendante (borne brune).
Le circuit est flottant. Il y a lieu de placer un pontage ou une résistance de 100 kΩ / 2W entre les bornes bleue et brune de l'appareil.
MISE EN OEUVRE
LA MECANIQUE
Le 222-064 étant obsolète, il est remplacé par le 754-6008.
Comme le montre la photo 3, la réalisation tout en gardant des distances minimales entre les divers modules est assez compacte.
Nous procéderons méthodiquement : Le marquage et perçage des différents points de fixation est fait à l’aide des cartes non montées. Nous commencerons donc par la mécanique et après l’étude du positionnement des différents modules, nous en viendrons à l’assemblage des modules proprement dits.
Agencement des modules
Les figure 9, photo 2 et photo 3 donnent une première indication quant à la disposition des divers éléments dans le chassis.
Le transformateur de 400 VA occupe la position centrale. Ses dimensions sont 90x115 mm à la base pour 121 mm de hauteur.
Comme l’espace disponible à sa base est de 110x120 mm, les dimensions sont assez critiques et doivent être spécifiées à la commande.
Plans cotés - Le châssis
Remarque préalable: les cotes ont été relevées avec précision sur notre réalisation, mais elles ne peuvent différer suivant les pièces en votre possession. Il est toujours prudent de n’effectuer les perçages que lorsque votre matériel est présent.
Ne sont données ici que les cotes qui permettent le positionnement exact et définitif des divers profilés. Une photo est associée à chaque dessin coté.
Les cotes de fixation des différentes cartes imprimées, du transformateur et du module relais ne sont pas mentionnées. Ces perçages doivent être marqués ‘’in situ’’ à l’aide de ces mêmes éléments.
Une petite contrainte supplémentaire: le nouveau boîtier 754-6008 nécessite d'usiner les profilés aluminium. L'espace entre les cornières et les capots fait 10 mm environ contre 20 mm pour le boîtier 222-064 ...
Châssis de dessous (Photo)
Châssis du haut – (Photo)
Faces avant et arrière
Les faces avant (plan et photo) et arrière (plan et photo) peuvent être usinées plus tard. Même remarque concernant la disparité des cotes suivant le matériel reçu (ventilateur, borniers, mètres …).
LES MODULES
La commande
Typon à l'échelle 1 , plan d'implantation des composants , photo de la carte. La carte mesure 90x145 mm.
Elle est fixée par quatre entretoises M-F de 10 mm au flanc droit du châssis (figure 12).
Le marquage des 4 trous de 3mm se fait avec grande précision à l’aide de la carte même. Ces 4 trous sont percés de manière à recevoir une vis M3 à tête conique.
Le côté femelle des entretoises se trouve du côté du flanc afin de pouvoir être vissé de l’extérieur à l’aide de 4 vis M3 (tête cônique-6mm de long). Ces vis ne peuvent dépasser la surface du flanc, car elles seront couvertes par les capots supérieur et inférieur.
Le raccordement de cette carte se fait par des cosses Fastonde 6,35 mm (type automobile) et des cosses ‘’picot’’ de 1,3 mm. Le trous de fixation devront être agrandis à 1,3 et 1,5mm pour permettre l’insertion. Les cosses doivent être placées en premier, les transformateurs en dernier.
Le radiateurs des IC2 et 3 sont des profilés en U 15x15x1,5 mm coupés en longeur de 25 mm. Ils sont positionnés à 5mm de la carte afin de ne pas provoquer de court-circuit avec les éléments voisins. Il y a lieu de préter attention au positionnement correct des nombreux composants polarisés.
Test de la carte de commande
La carte sera testée hors du chassis. Se référer au schéma de la carte.
Après avoir posé la carte à plat sur un support isolant, brancher le 230 Vac et vérifiez la présence des diverses tensions : +24 Vdc, -5 Vdc et les 10 Vdc du mètre (DPM).
La temporisation est contrôlée au point ‘’T’’. Connecter un multimètre et vérifiez qu’il y a bien 24 Vdc en ‘’T’’. Court-circuiter un instant les points ‘’R’’ et ‘’C’’ et vérifier que la tension en ‘’T’’ tombe bien à zéro pendant 3 secondes.
Débrancher le 230 Vac pendant une dizaine de secondes et re-brancher tout en contrôlant la tension au point ‘’T’’. Vérifier que la tension reste à zéro pendant 3 secondes.
Le fonctionnement du buzzer et du voyant de surcharge est testé en fin de réalisation.
Le relais statique
Le relais statique (photo) et la résistance R 51 de 330 Ω - 100 W sont fixés sur une tôle de 70 x 124 mm en aluminium de 1,5-2 mm ou en fer zingué de 1 mm (photo). Ces dimensions ne sont pas critiques.
Cette tôle sera ultérieurement fixée aux profilés arrières du châssis (figure 10, figure 11 et figure 13)
Il y a lieu de procéder au perçage des 4 trous dans la tôle et les profilés arrières conformément à la figure 10. Comme il y a quatre possibilités de fixation, il est utile de marquer la tôle par un détrompeur. Le relais statique et la résistance R51 viendront se loger sur la tôle entre les deux profilés. Attention, il y a juste la place !
Nous utiliserons pour le raccordement des fils des cosses à oeuil en soignant le sertissage.
Test du module relais statique
Il est préférable de tester le module avec une ampoule 230V/100W comme charge. Les bornes 3 et 4 recoivent la commande de la carte de commande (respecter les polarités). Les bornes 1 et 2 sont raccordées en série avec l’ampoule. La résistance de 330 Ω /100 W est connectée entre les bornes 1 et 2 (figure 18 et photo 9). Brancher d’abord le 230 Vac, ensuite l’alimentaion de la carte de commande. La lampe doit s’allumer faiblement pendant 3 secondes et briller ensuite.
Le transformateur
Deux cornières de section 40x20x2 mm sont fixées par 8 vis M3 à tête conique.
Le transformateur est positionné dans son support pour procéder au marquage. Nous utiliserons des vis M4 à tête conique (photo 4). Ces 12 vis ne doivent pas dépasser la surface des profilés car le capot inférieur vient immédiatement contre la cornière. Le transformateur sera fixé de manière à avoir les terminaux de raccordement tournés vers l’arrière de l’appareil.
Ce transformateur est fabriqué ‘‘sur mesure’’. Nous nous sommes fournis en Allemagne chez ‘’Wuesten’’
Il n’y a malheureusement pas de référence. Pour commander il faut en communiquer les spécifications.
Rappel : les dimensions de ce transformateur sont critiques !
Pour faciliter le test ultérieur des modules, il est préférable de raccorder d’emblée l’entrée 230 Vac par deux bons fils (rouges) de 1 mm de section et 750 Vdc d’isolation d’une longueur d’un mètre en vue de l’alimenter via un transformateur variable (Variac). Le secondaire est lui directement équipé du même fil et de deux cosses plates isolées rouges afin d’alimenter le module pré-régulateur.
La pré-régulation
Typon à l'échelle 1 , plan d'implantation des composants , photo de la carte. La carte mesure 160x80,5 mm.
Une découpe de 90x37 mm est prévue afin de recevoir le radiateur du transistor Q2 (photo).
Le transistor Q2 sera soudé de façon à ce que le sabot du transistor soit au bord de la carte et que le trou de fixation soit 20mm au dessus de la carte (figure 12). Le radiateur sera fixé en trois points aux profilés avant par des entretoises de 30mm en plastique et des vis nylon M4 de 40 mm (photo 3, photo 4 et figure 12).
Ce radiateur (ainsi que les deux autres) sont du type S41 à 1,2° C / Watt. Ils mesurent 88x100x35 mm et sont disponibles ‘’non-percés’’ entre autres chez Selectronic sous la référence 2032.
La carte sera maintenue par trois entretoises en plastique de 20mm et des vis nylon M4.
A noter la petite pièce en époxy qui recevra une des 3 fixations (photo 4).
Le marquage du trou de Q2 dans le radiateur se fait quand ce dernier et la carte sont en place. Notez également l’emplacement non critique du thermique (coupure à 70°C).
Attention, il ne faut pas que le radiateur reste attaché à la carte par le transistor lors des diverses manipulations. Les pattes de dernier fatiguent assez vite.
Au moment de la fixation définitive, nous ajouterons de la pâte thermo-conductrice sur le sabot du transistor.
Les cosses plates sont placées en premier et les trois électrolytiques en dernier.
Test du module
Pour ce faire, il est plus facile de travailler dans le châssis, avec le module monté.
Raccorder le secondaire 400 Vac du transformateur aux bornes situées près du pont redresseur et alimenter le primaire du transformateur par un autotransformateur variable (variac).
Le module doit être chargé par une des résistances de 20 kΩ / 50 W. Raccorder la résistance via 2 fils de 30 cm aux cosses ‘’HT’’ et ‘’M’’. Afin d’éviter les pinces ‘’croco’’ avec ce type de tensions, il est recommandé d’utiliser directement les cosses à sertir isolées rouges de 6,35 mm.
Placer un voltmètre (position 1000 Vdc) aux bornes de la résistance. Faire monter progressivement la tension. Celle-ci suivra la progression jusqu’à environ 530 Vdc. Vers 530 Vdc, la stabilisation doit se faire. Il y a lieu d’ajuster cette tension par la sélection de R9 ( 100 kΩ dans notre réalisation). L’emplacement de R9 peut également recevoir un potentiomètre vertical 10 tours (P1). Nous choisirons une valeur de 200 kΩ, et le règlerons au minimum avant d’alimenter la carte. La tension se stablisera alors vers 440 Vdc et nous ajusterons le potentiomètre (à l’aide d’un tournevis plastique) pour obtenir les 530 Vdc. A noter qu’une résistance fixe à 1% est plus fiable que le potentiomètre.
Avec 230 Vac au primaire du transformateur, nous avons 600 Vdc à la borne positive de C1 et sur le radiateur de Q2. Nous nous garderons bien de toucher à quoi que ce soit, toutes les tensions présentes sont potentiellement dangereuses.
Nous utiliserons le module de pré-régulation ainsi câblé pour tester le circuit de régulation.
La régulation
Typon à l'échelle 1 , plan d'implantation des composants , photo de la carte. La carte mesure 99x160 mm.
Le module régulation est le plus complexe à assembler. C’est d’ailleurs celui qui nous a donné le plus de fil à retordre. Mais procédons méthodiquement.
Le module est composé du circuit imprimé, de deux radiateurs S41 montés en vis à vis séparés par une entretoise de 30 mm, et d’une plaque époxy (99x140 mm) qui supporte les deux radiateurs (voir photo 4 et photo 13).
Les radiateurs sont fixés à cette plaque par quatre petites équerres coupées dans une cornière aluminiun de 10x10x1,5 mm (photo 15).
Avant d’assembler la carte, il y a lieu de positionner ce petit monde dans le châssis.
Les figure 9 et figure 13 sont assez parlantes. La première opération est le marquage-perçage des 2 fixations de la carte de régulation dans la cornière avant. Nous positionnerons cette carte bien au milieu entre la carte de pré-régulation et l’oreille du coté gauche (photo 4).
La seconde opération est le marquage-perçage de la plaque époxy qui sera fixée sur les deux profilés carrés dans l’alignement exact de la carte (voir figure 13). Nous fixerons ensuite les 4 petites équerres au bas des radiateurs selon la figure 13 (photo 15).
Avant-dernière opération, la plus délicate : le positionnement des 2 radiateurs.
Nous les fixerons l’un à l’autre par l’unique entretoise de 30 mm avec une vis M4 métallique (temporairement !). Positionner l’ensemble sur la plaque époxy, le bord avant des radiateurs étant aligné sur le bord arrière du profilé carré comme montré sur la figure 13 et bien centré par rapport à la carte de régulation. Marquer et percer …
Dernière opération : le marquage des trous de fixation de Q2 et Q3. Les trous se trouvent à 50 mm de haut (figure 13), l’autre dimension est marquée au mieux en se référant à la broche centrale des transistors sur la carte.
Le module terminé, la carte de régulation est bien parallèle à la plaque époxy, et se trouve dans le prolongement exact de l’ailette horizontale du radiateur. (photo 13)
Les thermiques sont fixés à l’arrière des radiateurs. Remplacer la vis M4 métallique par une vis en nylon.
Lors de l’assemblage définitif, ne pas oublier la pâte thermo-conductrice sur Q2 et Q3. (photo 14)
Test du module
Phase 1 : Court-circuiter les 3 cosses 1,2 et 3. et raccorder la masse et les –5 Vdc et +24 Vdc.
Mettre le module commande sous tension.
La tension aux 3 cosses doit être de +8,2 Vdc environ. Vérifier que cette tension se retrouve bien sur R4 (470 Ω). Mettre hors tension le module de commande.
Phase 2 : Maintenir les 3 cosses 1,2 et 3 court-circuitées.
Raccorder la sortie ‘’HT’’ et la masse du pré-régulateur à la cosse ‘’+’’ d’entrée du régulateur (près de C12) et à la masse ‘’M‘’
Débrancher la résistance de 22 kΩ / 50 W du pré-régulateur et la raccorder à la sortie du régulateur entre les cosses "POS" et "NEG".
A l’aide du variac, faire monter progressivement la tension du transformateur. Vers 250 Vdc de sortie du pré-régulateur, la tension aux bornes de la résistance doit se stabiliser. C’est le résultat des 8,2 Vdc présents sur R4.
Poursuivre la montée en tension jusqu’à 230 Vac. La tension d’entrée est alors de +530 Vdc sur le radiateur de Q2. Vérifier que la tension sur le radiateur de Q3 se place à mi-chemin entre la tension d’entrée de 530 Vdc et la tension de sortie de 250 Vdc, soit vers 390 Vdc. Si c’est le cas : tout fonctionne et on peut passer au câblage définitif.
Nous nous garderons bien de toucher à quoi que ce soit, toutes les tensions présentes sont potentiellement dangereuses.
LA FINITION
Les modules sont fixés définitivement dans le châssis. Comme vous l’avez constaté, le raccordement des divers éléments se fait par cosses. Il n’y aura rien à souder puisque le transformateur est déjà équipé de ses fils.
Les fils de raccordement qui transportent de la haute tension sont à âme multibrin et doivent avoir une section de 1 mm² minimum et être protégés par un bon isolant. (Ex : réf. 8178-5 de Selectronic pour un diamètre extérieur de 2,6 mm et une isolation de 750Vdc)
Les faces avant et arrières sont câblées avec un peu de mou de manière à permettre la dépose à plat des faces.
Pour des raisons d’isolation, les trois bornes de sortie ne sont pas fixées directement dans la tôle de la face avant : une ouverture est pratiquée dans la tôle et une pièce de 68x30 mm en Tufnol de 4 mm (ou en bakelite) est fixée sur la face qui reçoit les trois bornes. Le Tufnol se vend par plaque de 285 x 590 mm chez Radiospares (N° de stock : 374-418).
Les terminaux des portes fusibles doivent être isolés avec de la gaine thermo-rétractable. Le ventilateur est placé à l’extérieur du boîtier, et pulse l’air vers l’intérieur.
La résistance de charge R22 et le buzzer sont placés sur un support composé de deux cornières de 15x15x1,5 mm maintenues par une tôte aluminium de 2 mm.
La photo 5 montre ce support en place. Par facilité, les quatre vis de maintien sont fixées au châssis ‘’écrous vers le haut’’ (photo1, figure 11, figure 12 et figure 13). La résistance R22 de 22 kΩ / 50W se trouve dans le flux d’air du ventilateur. Elle est raccordée entre les bornes de sortie "POS" et "NEG".
Nouvelle mise sous tension
Il est préférable d’alimenter directement la carte de commande en 230 Vac et d’alimenter l’appareil via le plug secteur à l’aide du variac.
Régler le potentiomètre P50 au minimum et monter progressivement la tension. La sortie doit se stabiliser vers 50 Vdc. Continuer à monter la tension jusqu’à 230 Vac.
Le réglage de P50 doit maintenant pouvoir faire varier la tension sur toute la gamme.
Si la gamme ne s’étend pas de 50 à 450 Vdc, il est toujours possible de changer légèrement les valeurs de R1 et R3.
L’appareil est alors pleinement fonctionnel. Rebrancher la carte de commande et alimenter normalement.
A l’aide d’un tournevis plastique, ajuster P2 et P3 pour la valeur exacte des tension et courant aux afficheurs. Ce réglage sera refait définitivement après 1 heure de fonctionnement à 350 Vdc et à 350 mA à l’aide d’un multimètre extérieur.
N’oubliez pas que la précision de ces afficheurs fait +/- 0,5 % au maximum.
Le moyen le plus facile est d’utiliser 4 ampoules de 230 V 60 W (2 branches parallèles de 2 ampoules en série, soit 460 Vac et 240 W !). Attention avec les ampoules, leur résistance à froid est considérablement plus faible. Lorque vous les branchez, programmer l’alimentation à 50 V sous peine de claquer le fusible rapide de 0,5 A.
Les masses
L’ensemble des circuits est flottant. La borne bleue est raccordée à la masse des circuits. La borne brune est raccordée au châssis et à la ‘’Terre’’ du socle 230 V. On s’assurera que toutes les parties du chassis sont bien en contact électrique.
LES MESURES
Pour les mises au point et les mesures, nous nous sommes fabriqués une charge de 1000 Ω - 200 W montée sur un refroidisseur. (photo 18)
Cette charge qui avait déjà subi bien des sévices au cours de mises au point a expiré définitivement à l’occasion d’un appel téléphonique qui m’avait temporairement éloigné de mon banc de test …
Toutes les mesures sont effectuées à 300 Vdc et 300 mA. Nous décrivons ici les mesures les plus délicates, à savoir la résistance interne, l’impédance interne et le facteur de bruit.
Résistance interne
L’alimentation débite 300 mA dans la charge de 1000 Ω. A l’aide d’un interrupteur, on ajoute une résistance de 3000 Ω qui provoque une augmentation instantanée de courant de 100 mA (figure 23).
La variation de tension (figure 24) est de 50 mV dc (à 300 Vdc).
Ceci nous donne une Ri = U/I soit 0,05/0,1 = 0,5 Ω.
A noter que la résistance série R15 qui mesure le courant, y participe pour 0,22 Ω .
Impédance interne
Un signal de 3 Vac est injecté au pied de la charge (figure 23). La signal alternatif ‘’Vm’’ apparaissant aux bornes de sortie nous permet de calculer l’impédance interne par la formule : Zi (Ω)= 1000 x Vm/3
Les valeurs mesurées sont (photo 19) :
Fréquence
|
Signal mesuré
|
Zi
|
10Hz
|
1,4 mV
|
0,47 Ω
|
100Hz
|
1,4 mV
|
0,47 Ω
|
1kHz
|
2,4 mV
|
0,8 Ω
|
10kHz
|
1,4 mV
|
0,47 Ω
|
100kHz
|
1,7 mV
|
0,57 Ω
|
C’est ici que nous constatons le bénéfice de la contre-réaction du circuit de régulation. En effet sans cette contre-réaction, l’impédance interne serait de l’ordre de 4 Ω. Si nous enlevons les 0,22 Ω de la résistance R15 qui se trouve en dehors de la boucle de contre-réaction, la valeur réelle de Zi est de l’ordre de 0,3 Ω. La contre-réaction améliore donc la résistance et impédance interne d’un facteur 10.
Facteur de bruit
La sortie de l’alimentation programmée à 300 V / 300 mA est mesurée en AC.
Vérifier que votre millivoltmètre AC et oscilloscope supportent bien une telle tension DC à leur entrée, sinon il y a lieu d’intercaler une cellule C-R (ex : 47 nF-1000 V et 1 MΩ) pour éliminer la composante DC.
La tension AC mesurée est inférieure à 200 µVAC (photo 20).
200 µVeff sur 300 Vdc nous donne un rapport de 0,67x10-6 soit 123 dB.
Spécifications
Liste des composants
Nomenclature complète
CONCLUSION
Las de travailler avec un auto-transformateur variable et un système redresseur non stabilisé, nous nous sommes d’abord tournés vers les fabricants de matériel professionnel. Mais au vu des prix rédhibitoires pour l’amateur, lentement l’idée d’une réalisation personnelle a mûri. Ce projet a été finalisé il y a plus de dix ans et est en service presque quotidien. Il se révèle d’une robustesse étonnante, aucune panne n’est encore survenue. Seul le fusible rapide de 500 mA fait régulièrement les frais de nos maladresses.
Besoin d'un complément d'information ?
Envoyez un courriel à l'adresse: This email address is being protected from spambots. You need JavaScript enabled to view it. - End of text -Récapitulatif des photos (Haute définition)
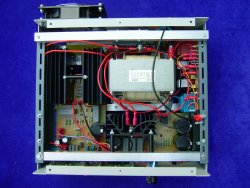
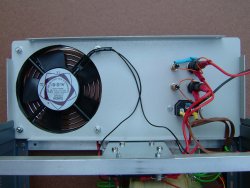
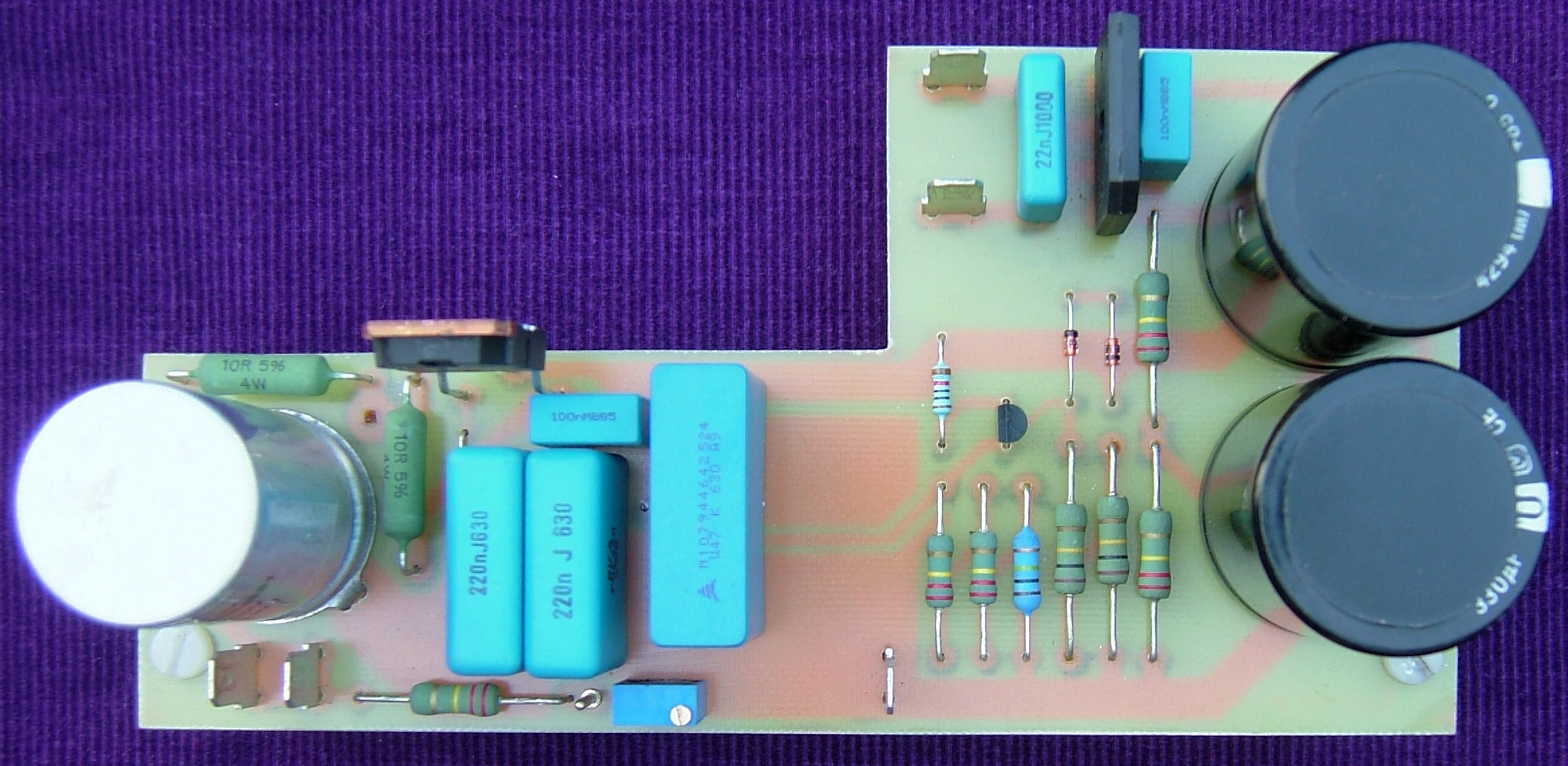
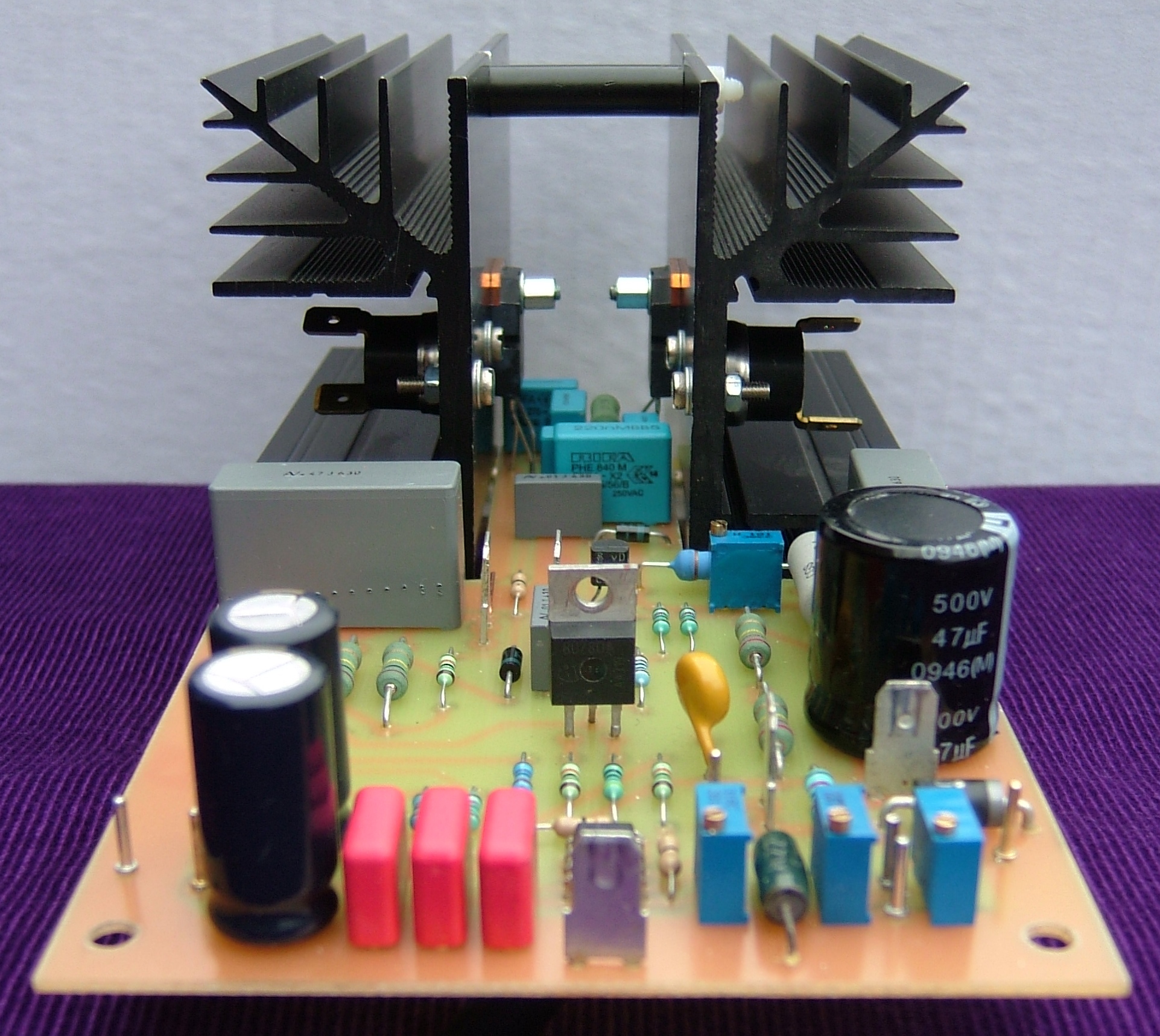